Positive Displacement Pipetting
The core principle of the positive displacement (PD) technology involves a piston-like plunger integrated within the pipette tip. As the plunger moves upwards, making direct contact with the liquid, it creates a vacuum that draws liquid into the tip. When the plunger moves downwards, it expels the liquid. This direct interaction between the plunger and the incompressible liquid ensures that the plunger movement translates directly into the volume of liquid aspirated or dispensed, guaranteeing precise and accurate pipetting. Formulatrix has leveraged this gold standard pipetting method in two of its liquid handlers - automating positive displacement technology in a way that’s scalable, affordable, and remarkably precise.
- Reproducibility: Eliminating the air gap eliminates variables from the pipetting equation. Each plunger movement creates a directly proportional volume displacement, resulting in precise transfers for reproducible results, even at very low volumes.
- No Cross-Contamination: Tips are disposable and the plunger seal isolates the liquid from the pipette hardware, leaving no path for aerosols.
- Liquid Class Agnosticism: Direct contact between the liquid and the plunger removes the variable effects of fluid liquid properties such as viscosity, surface tension, and volatility. Precision and accuracy are maintained for all liquids with no need for liquid class adjustments. In addition, viscous liquids can be transferred much faster than on air displacement systems, without compromising accuracy.
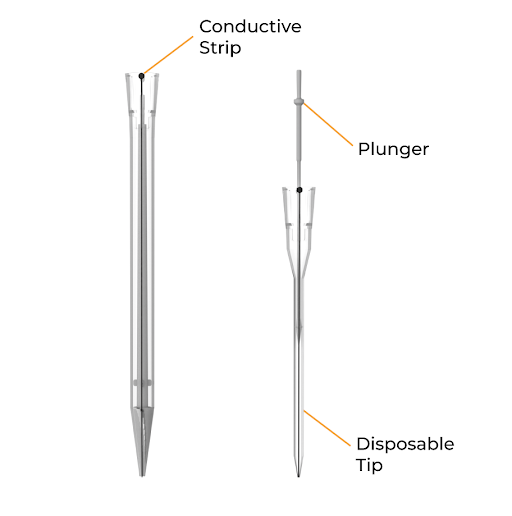
Formulatrix’s Innovative Positive Displacement Liquid
Handling Technology
We have developed innovative automated liquid handlers, the F.A.S.T. TM and the FLO i8® PD with positive displacement technology, featuring the following advancements:
Wide Volume Range PD tips
The F.A.S.T. uses 13 µL and 50 µL tips while the FLO i8 PD uses 50 and 1000 µL tips, providing a wide range of volumes (0.1 µL to 1 mL) with unmatched accuracy and precision.
Smart Positive Displacement Tips
The FLO i8 PD has transparent conductive positive displacement tips suitable for a variety of workflows, covering a wide volume range of 0.2 µL to 1000 µL with precision (CV <2.5% at 1 µL).
- Dynamic Liquid Level Detection: These tips use the conductive stripes on their sides to provide resistance-based liquid-level detection and tracking without prior definition of labware well profiles.
- Non-Contact Dispensing: In addition to contact liquid transfers, the FLO i8 PD can perform non-contact liquid dispensing using the same channels and tips. This dramatically increases the throughput capability of the instrument. Consequently, a single instrument can automate liquid handling for workflows that involve both dispensing and transferring.
96-Channel Positive Displacement Head
The 96-channel head of the F.A.S.T. liquid handler coupled with positive displacement tips offers unparalleled speed, flexibility, and efficiency.
- Throughput: It facilitates rapid sample transfers in 96- and 384-well plates, making it ideal for high-throughput assays.
- Tip Selection: It allows user to select and pick up between 1 and 96 tip(s), eliminating the need for multiple pipetting heads. This helps to accommodate various experimental needs and improve workflow efficiency.
- Tip Clamping: Formulatrix's zero-insertion force tip clamping mechanism ensures a reliable sealing interface between each pipette tip and the head.
8 Independently Spanning Channels
All eight channels in the FLO i8 PD are independent in span, z-axis, and volumes. They are further equipped with touch sensors that help locate labware bottom and detect collisions. The channels and tips combined can handle liquids from labware with a height of up to 140 mm, making the FLO i8 PD an excellent choice for aliquoting, plate reformatting, and general-purpose liquid handling.
Computer Vision
Both of our positive displacement instruments are equipped with advanced computer vision technology, enabling precise detection and management of the number of tips in use. This feature enhances operational precision and reliability, ensuring optimal performance in every application.